Asphalt paving is a durable material that stands up well to traffic and environmental conditions. It is also eco-friendly and recyclable, reducing demand for new raw materials and cutting energy costs.
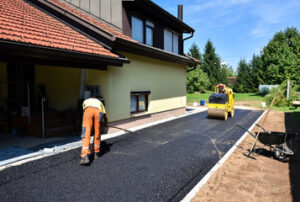
Its quick installation and curing process allow for fast construction times, minimizing disruption to travelers and local businesses. This makes it an ideal choice for time-sensitive projects. Contact Charleston Paving Solutions for professional help.
Asphalt isn’t simply poured on the ground. It requires layers of materials that support it and make it able to handle heavy loads. A quality paving contractor will carefully consider the pavement design and thickness needed for each job. For instance, a heavily trafficked road or commercial parking lot will require much thicker asphalt than a residential driveway. This is important because the thickness of asphalt relates directly to its strength and durability.
The first layer is a gravel base that is placed on the site and compacted using a roller. This creates a stable foundation for the asphalt surface and helps to distribute the weight of vehicles evenly across the road or parking lot. This can prevent premature wear and tear from a single point of stress or weight, as well as damage to the underlying soil.
Next, a layer of crushed rock is added. This provides drainage and further supports the paved area. The layer should be a minimum of 4 inches deep, and it is recommended that it be 6 inches in heavy traffic areas. This will ensure the paving lasts longer and prevents fatigue cracking that can eventually undermine the entire surface.
The final layer is the asphalt mix. This is typically composed of a mix of aggregate (such as gravel or sand) bound together with bitumen binder, which is derived from crude oil. The aggregates are selected based on their size and other qualities, and they’re dried before being mixed with the bitumen. The mixture is then heated to a specific temperature for ease of working and compaction. It is also inspected at this time to ensure that it meets all specifications.
Mixing
Asphalt paving comes with its own jargon, and it’s important to understand the terminology in order to make informed decisions about your project. A few key terms you’ll want to know include dense-graded mix, warm mix, and recycled materials.
Asphalt is a mixture of aggregates (like crushed stone, gravel, and sand) and a dark, petroleum-based substance called bitumen. This sticky, black substance binds the aggregate together to create a strong and durable pavement.
Different asphalt mixes are used for various projects and weather conditions. The most common is Hot Mix Asphalt (HMA). It’s the’standard’ asphalt mix that’s typically used for roads, highways, and freeways. HMA is extremely durable, resistant to water infiltration, and has a low maintenance cost.
During the mixing process, aggregates are combined and heated in an asphalt plant. The temperature of the asphalt is critical because it needs to stay hot throughout the paving process. If it cools, the paving will not be able to be compacted.
To keep the asphalt at a suitable temperature, it may be emulsified in water with an emulsifier before being mixed with aggregate. This makes cold mix asphalt (CMA) less viscous and easier to work with, especially when making repairs. However, CMA isn’t as durable as HMA or WMA, so it’s typically only used for patching and lesser-trafficked service roads.
Some plants also use recycled material to add to the asphalt mixture. This helps reduce the amount of new materials needed and saves on construction costs. Additionally, using reclaimed material allows the asphalt to be repurposed in future paving projects, further reducing waste and saving resources. Adding recycled materials also allows the asphalt to maintain a higher level of durability and performance.
Applying
Asphalt paving is a crucial part of many basic construction projects, including roads, driveways, and parking lots. Its durability and versatility make it a popular choice for high-traffic areas that need to withstand the weight of vehicles and other heavy loads. However, it’s important to understand the process of installing asphalt to ensure a quality surface that lasts.
The first step in the paving process is to clear the area of any debris or obstacles that could prevent the proper installation of the asphalt. This typically involves the use of heavy equipment like bobcats and front loaders to remove any existing surface and prepare the ground for paving. In addition, the subgrade must be properly prepared to achieve stability and support the asphalt. This usually requires excavating the ground to a suitable depth and then compacting it to achieve uniformity and stability.
Once the site is cleared, the asphalt mix can be poured. This typically includes a mixture of aggregates, binder, and fillers. The aggregates, which may include crushed stone or sand, provide strength and stability to the pavement. The binder, which is normally asphalt cement, acts as a glue that binds the aggregates together. The fillers, which can be fine aggregate or dust, are used to fill any voids in the mixture and ensure a smooth, even surface.
After the mix is spread and compacted, it must be inspected for quality and consistency. If necessary, minor adjustments can be made at this stage to ensure the desired results. Once the paving has been completed, it’s important to ensure that traffic is carefully managed while it cures. Failure to do so can result in damage, cracking, and potholes. However, using maintenance techniques like crack sealing can help reduce these issues and prolong the lifespan of the asphalt.
Compaction
An asphalt pavement’s structure depends on how tightly it is compacted. The more it’s compacted, the stronger and more resilient it will be against rutting and other forms of premature failure. This is why it’s so important to hire a contractor who understands and practices proper compaction techniques.
During the paving process, the hot asphalt mix must be compacted as it is laid on the surface. This is done with rollers, which are designed to reduce air voids and create a dense, firm structure. A good contractor will use a combination of different types and sizes of rollers, depending on the project requirements. They will also use non-destructive methods to measure moisture content in real-time, ensuring that the rollers are always operating at optimal conditions.
The first step in the process is to compact the unsupported edge of the pavement. This is usually accomplished using a vibratory steel wheel roller. While a pneumatic roller can also be used in this stage it is less effective because of the way that it pushes the asphalt mix sideways. This type of movement is called a bow wave and it can cause the mix to crack longitudinally as well as laterally, widening the mat beyond the edge.
The goal is to achieve a uniform material density, which requires precise timing between the paver and the breakdown roller. This is because the breakdown roller must be able to complete its work before the asphalt mix cools below a temperature consistent with achieving desired material density. The exact target temperature varies based on the recipe used and the thickness of the layer being constructed. It is also influenced by ambient air temperatures and wind velocity.
Inspection
Paving is a process that uses concrete, bricks, or natural stone to create a hard, solid surface for roads and driveways. It offers a variety of customization options for aesthetics, but requires significant maintenance. Asphalt, on the other hand, is a petroleum-based composite that offers durability and cost efficiency. It’s a great choice for road construction, and is able to withstand traffic, weather, and other environmental factors.
Regardless of which material is used, all pavements need regular maintenance to extend their lifespans and keep them looking new. The elements of rain, snow, sun, heat and cold can cause asphalt surfaces to break down or degrade over time. To help minimize these effects, preventative maintenance, like crack filling and seal coating, is essential.
Cracks in asphalt can easily become potholes or larger areas of deterioration if left untreated. This is why asphalt surface maintenance includes inspection, cleaning and filling of these fissures. Proper crack sealing can help protect and extend the life of asphalt, especially when it is seal coated regularly.
The paving industry uses various testing methods to ensure consistent mix design, compliance with specifications and quality of the finished product. These tests also play a crucial role in predicting pavement performance, preventing failures and saving costs over the lifetime of the pavement.
While asphalt may seem like a simple, ingenious invention, it’s actually an exceptionally complex and multifaceted material. Understanding its composition and paving process is a fascinating look at the intricate work that goes into making our roads, driveways, and parking lots safe and functional. To ensure that your paved surfaces are as durable and long-lasting as possible, invest in asphalt services such as resurfacing, crack repair and sealcoating.